PLASTİK ENJEKSİYON KALIPÇILIĞINDA DİESEL ETKİSİ VE MOLDEX3D İLE ÇÖZÜM YOLLARI
Giriş
Plastik enjeksiyon kalıpçılığı ile üretilen ürünlerin kalite kriterleri genellikle geometrik ve ölçüsel kriterler öncelikli olarak incelenir. Ancak beyaz eşya, otomotiv gibi son kullanıcıya hitap eden sektörlerde ürünlerin görsel kalitesi de kalıplama başarısı açısından önemli rol oynamaktadır.
Plastik enjeksiyon kalıp tasarımcıları ürün görsel yüzeylerinde problemsiz ve hatasız üretimler elde edebilmek için çeşitli bilindik metodlara başvurarak kalıp tasarımı yapmaktadırlar. Örneğin enjeksiyon giriş memeleri ürünlerin göz önünde olmayan yüzeylerine saklanırken, kalıp içerisinde eriyik birleşim bölgelerinin görsel yüzeylere denk gelmemesine dikkat edilmektedir.
Bazı görsel kusurlar ise öngörmesi çok daha zor mahiyette karşımıza gelebilmektedir. Örneğin literatürde Diesel Etkisi olarak bilinen kalıplama problemi de bunlardan bir tanesidir.
Diesel Etkisi Nedir?
Plastik enjeksiyon kalıpçılığında ortalama 40C ile 60C derece arasına ısıtılmış olan kalıp içerisine 180C ile 240C arasındaki eriyik haldeki plastik yüksek basınç ile mümkün olan en kısa sürede dolum için enjekte edilir. Bu sırada 60C’lik kalıp boşluğunu doldurmuş olan hava kalıp içerisinde ilerleyen plastik akışı sebebi ile itilerek kalıp aralıklarından dışarıya çıkmaya zorlanır.
Kalıp tasarımında kullanılan lokmalar, insertler, iticiler ve ayrım yüzeyleri gibi bölümler havanın çıkışı için ideal aralıkları oluşturmaktadır. Ancak kalıbın tasarım sınırlandırmaları, havanın kaçışı için gerekli olan bu gibi unsurları çokça içermeye izin vermeyebilir.
Kalıp tasarımızda hava kaçışı için aralıklarımızın olmadığı ve yüksek sıcaklıklarda büyük kalıp hacimlerini doldurduğumuz durumlar Diesel Etkisi oluşumu için en kritik durumları oluşturmaktadır. 1 saniye gibi çok kısa süreler içerisinde yüksek hız ve basınçla kalıp hacmini doldurmaya çalışan plastik hava hacmini kalıp içerisinde ilerlemeye zorlar. Hava kendisine aralıklar bulun kalıp hacmini terk edemediği durumda ise ilk hacminin %2 ila %5’i hacimlere sıkışmak zorunda kalır. Termodinamikten bildiğimiz aşağıdaki formüle göre hacim 50 ile 20 kat arasında azaldığında hava basıncı da benzer oranlarda artacak ve bu da sıkışan havanın sıcaklığını enjeksiyon kalıpçılığı için uygun olan sıcaklık aralıklarının çok üzerine taşıyacaktır. Bu yüksek sıcaklıkta havanın temas halinde bulunduğu yüzeylerde yanma kusurları oluştururken, yüksek basınçlı hava kalıp boşluğunun da dolmasına engel olacaktır. Aşağıda Diesel Yanması görülen bazı plastik parça örnekleri verilmiştir.

Örnek Üretim Uygulaması : 4 Gözlü PBT Endüstriyel Fiş Kalıbı
Tasarımı aşağıda görülen %15 Cam Elyaf katkılı PBT (Polibütilen Tereftalat) polimer malzemeden üretilecek Endüstriyel Fiş’in 4 gözlü bir kalıpta üretilmesi planlanmaktadır. Elektrik kabloları ve pimleri erkek kalıp üzerine yerleştirilerek Insert üzerine enjeksiyon yapılarak birleşimin sağlanması planlanmıştır.
Kalıp içerisine enjekte edilen PBT Malzeme için 260 C eriyik sıcaklığı planlanmış ve kalıp 70C sıcaklığa şartlandırıcı üzerinden ayarlanmıştır. Kalıp içerisinde daha sonra Moldex3D’de yapılan analizler ile aşağıdaki şekilde plastik akışı gözlemlenmiştir.
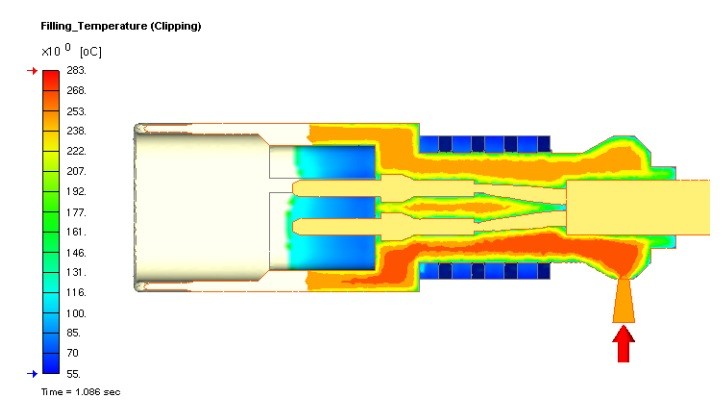
Kalıp içerisinde bulunan hava 1 saniyelik dolum süresinin sonunda fişin ağız kısmına doğru ötelenmiş ancak bu bölgeden bir çıkış aralığı bulamamıştır. Havanın basınç ve sıcaklığının yükselmesi sonucunda gözlemlenen Diesel Etkisi sonucunda hem PBT malzeme kalıbı dolduramamış hem de dolmayan kısımda yüzey bozukluğu oluşturmuştur. Ancak elektrik sektörün yoğun olarak kullanılan PBT malzemenin yüksek ısıl direnci yanık oluşumunun bu örnekte önüne geçmiştir.

Çözüm Önerileri
Diesel Etkisi gibi problemleri enjeksiyon öncesinde ön görebilmek için Moldex3D gibi simülasyon yazılımları kullanmak gerekmektedir. Ancak üretilmiş ve geri dönülmez yollara girilmiş kalıp devreye alma süreçlerinde uygulanabilecek az çözümden bir tanesi ilgili sıkışma bölgesinde ek ventilasyon (hava kaçış kanalları) oluşturmakdır. Bu örnek Endüstriyel Fiş Kalıbı için önerilen hava kaçış kanalı tasarımı için kalıp içerisine işlenecek ek ventilasyon figür CAD çizim olarak aşağıda verilmiştir.
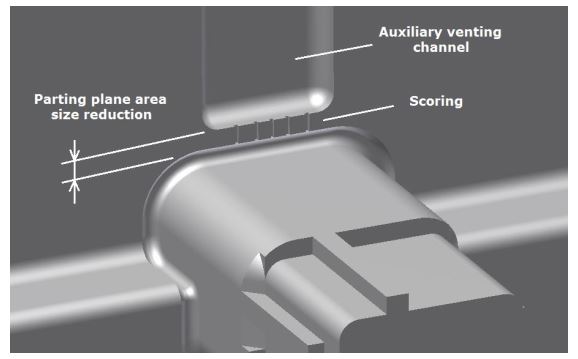
Moldex3D İçerisinde Diesel Effect Problemlerinin Tasarım Aşamasında Tespiti
Moldex3D içerisinde yapılacak başlangıç Dolum analizlerinde dahi bir kaç ek seçeneği aktif hale getirerek tasarladığımız kalıpta Diesel Effect oluşup oluşmayacağını görmek mümkündür. Bunun için Venting menüsü altından venting analizi aktif hale getirilir ve kalıp içerisinde enjeksiyon öncesi havanın sıcaklığı ve basıncı girilir. Bu noktada sıcaklık genelde dış ortam sıcaklığı ve basınç atmosfer basıncı olarak alınabilir. Kalıp kapandıktan sonra dolum başlayana kadar geçen 4-5 saniyelik sürede havanın kalıp yüzeyi ile temasında çok da ısınmayacağı kabul edilebilir.
Kalıp içerisined havanın kaçabileceği aralıklı yüzeyler, örneğin lokmalar, insertler, iticiler ve ayrım yüzeyleri gibi bölgeler var ise bu bölgeler Moldex3D içerisinde ventilasyon yüzeyleri olarak tanımlanır. Analiz çalıştırılarak dolum analizi sonuçları arasında kalıp içi sıcaklık dağılımlarına bakılarak ek ventilasyon ihtiyacı var mı kolayca tespit edilir. Böylece Endüstriyel Fiş örneğinde yaşandığı gibi ek kalıp revizyonu ihtiyaçlarına gerek kalmadan, para ve zaman kayıplarını bertaraf ederek devreye alım süreci tamamlanmış olur.
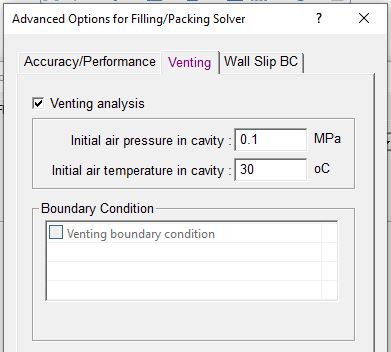
Referanslar:
- Diesel Effect Problem Solving During Injection Moulding, Miroslav KOŠÍK, Lukáš LIKAVČAN, Jozef BÍLIK, Maroš MARTINKOVIČ1, 2014
- ALFREDO, C., E. The Complete Part Design Handbook – For Injection Molding of Thermoplastics. Ohio: Hanser Gardner Publications, Inc. ISBN 13: 978-1-56990-375-9, ISBN 10: 1-56990-375-1
- KAZMER, D. O., R. 2007. lnjection Mold Design Engineering. Munich: Carl Hanser eISBN: 978-3-446-43419-6, Print ISBN: 978-3-446-41266-8
- MENGES, G., MICHAELI, W., MOHREN, P., R. 2001. How to Make Injection Molds. Munich: Carl Hanser Verlag. ISBN: 1-56990-282-8, ISBN: 3-446-21256-6